By Stephen DeAngelis
Even before the Covid-19 pandemic disrupted global supply chains and upended the global economy, supply chain experts insisted that supply chain resilience was essential. Back in 2019, Joseph Shamir, Founder of ToolsGroup, wrote, “If the last decade has taught us anything, it’s to expect the unexpected — from extreme weather events to endless political psychodramas to tech startups disrupting whole industries. Global supply chains are particularly vulnerable to changes triggered by these events, including increased regulation, new tariffs and radical shifts in demand patterns. [There is a] need to prepare supply chains not only to survive, but to thrive in chaos.”[1] Little did Shamir know that only a few weeks later, the pandemic would be grabbing all the headlines. Nevertheless, his point is well made — supply chains need to thrive in chaos. To do that, they must be resilient. According Matt Stekier and Aaron Ennest, supply chain experts at Plante Moran, the need for resilience is nothing new; however, the urgency to make supply chains resilient has never been greater. They explain, “Efforts to make supply chains stronger are as old as supply chains themselves, but today’s global networks necessitate a more proactive, continual, and detail-oriented approach. Even if you have a resiliency plan in place, now is the time to reassess your preparedness.”[2]
Addressing Supply Chain Resilience
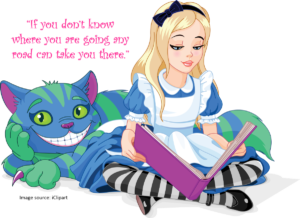
Lora Cecere, founder of Supply Chain Insights, insists that too many of today’s supply chain professionals are like Alice in Wonderland asking for directions from the Cheshire Cat. She writes, “When you ask most supply chain professionals to define resilience, the question stops the person in their tracks. The reason? We are not clear on definition. I define supply chain resilience as: The ability of an organization to deliver reliable and consistent results for revenue, margin, customer service, and quality in the face of demand and supply variability. … So, if you use [my] definition, you might ask, how are we doing commercially against this goal? Interestingly, in Q3 2023, 38% of manufacturers, distributors and retailers missed their target for revenue guidance for the quarter. … My conclusion? If businesses cannot accurately forecast revenue, the organization is not resilient.”[3] She adds, “I would like for organizations to be more proactive to sense, respond, and adapt. Today, this is not the case.”
Being proactive, like Stekier, Ennest, and Cecere suggest, requires a starting point for the resilience journey. Nathan Feather, Chief Financial Officer at PrimeRevenue, explains, “While it is impossible to know exactly how the economic and supply chain landscape will shift and transform over these coming months and years, there are lessons and principles you can bet on to hold true — regardless of what that landscape looks like — and serve the best interests of the companies that follow them.”[4] He offers three principles that he believes apply to companies whose business and success largely rely on the health of their supply chains. They are:
Principle One-Liquidity: According to Feather, “Liquidity is crucial in both economic times and bad. When business is booming, easy access to liquidity and cash flow provides the flexibility and capability to take smart risks and seize on timely opportunities, along with the security and peace of mind of knowing your business is well-positioned to handle any changes in the economic tides. Meanwhile, in periods of volatility, available liquidity can very well be your company’s lifeline that allows for continued investment, hiring, and growth.”
Principle Two-Surprise: Feather writes, “The biggest supply chain threat [is] the one you don’t know about. … The truly biggest risks and threats — to the global economy, to businesses, and to supply chains — are the ones you’re unaware of and not accounting for in the first place. When it comes to risk management, assessing the likelihood of various outcomes, and preparing accordingly, is vital. But what’s even more vital? Preparing accordingly for the uncertain, the unknown, and the unpredictable.” One way to deal with surprise is leveraging war gaming techniques. For example, Enterra Business WarGaming™ enables organizations to leverage their data to make strategic decisions by anticipating the moves of their competitors and taking direct action to beat the competition, mitigate risk, navigate uncertainty, and maximize market opportunity. Part of Enterra Business WarGaming is the Enterra Global Insights and Decision Superiority System™ (EGIDS™) — powered by the Enterra Autonomous Decision Science™ platform — which can help business leaders rapidly explore a multitude of options and scenarios.
Principle Three-Preparedness: Feather insists companies should “invest in preparedness, not prediction.” He adds, “[That] quote is from Nassim Taleb, author of multiple books on risk and uncertainty. So, what does investing in supply chain preparedness look like? It can look like using supply chain finance as a lever to free up cash flow, and it can also look like allocating resources toward initiatives such as geographical diversification, the creation of inventory buffers, sustainability, and artificial intelligence. These measures help build supply chain resilience — and essential to resilience is not depending on any particular scenario or outcome playing out, but being prepared regardless of the economic forecast and climate ahead.”
Actions to Consider
• Map the supply chain. Paul Maplesden, Lead Content Strategist for Logistics and the Supply Chain at GEODIS, explains, “Mapping out key supply chain partners, routes and other factors is a good first step toward resilience. It enables supply chain leaders to better understand how their company’s goods flow from suppliers to consumers.”
• Conduct end-to-end supply chain risk assessments and prioritize important focus areas. Mapping helps a company understand their end-to-end supply chain so that risks can be assessed. Journalist Sean Galea-Pace reports that conducting end-to-end supply chain risk assessments and prioritizing important focus areas is the first of several suggestions offered by EY analysts to help companies improve their end-to-end supply chain and operations strategy to grow, optimize and protect operations. Galea-Pace writes, “Responsiveness and speed are fundamental. Proactively engage with supply chain ecosystem partners, like suppliers and logistics service providers (LSP) to conduct a risk check.”[6] During that check do the following three things: 1) Identify: Identify changing demand and inventory levels in order to work out critical gaps in supply, production capacity, warehousing and transportation. 2) Define: Work out common goals and an actionable short-term and outcome-driven resilience strategy with breakdown activities among the supply chain ecosystem. 3) Deploy: Create action plans based on scenario analysis to decrease the impact of disasters.
• Develop a robust risk management process and diversify supplier network. According to the EY analysts, “Companies should develop a methodology to measure risk for each supply chain node, warehouse, factory, supplier or transportation node.” Maplesden adds, “Supplier relationship challenges are an unavoidable reality, but being proactive boosts resilience. A supply chain map identifies current suppliers. Leaders can use that to create options and alternatives so they don’t become overly dependent on a single supplier. … As with alternate suppliers, backup carriers and routes can help make a supply chain more resilient. International networks are easily disrupted by black swan events such as piracy, bridge collapses, blocked routes and pandemics, so having contingencies in place is vital for a healthy supply chain.”
• Implement digital and automated manufacturing. Transforming into a digital enterprise is becoming an imperative in today’s business environment. EY analysts urge, “Introduce a strong manufacturing excellence program to mitigate reliance on labor intensive processes. This will enable standardization of daily work and job aids, decreasing the pressure of relying on individuals to make an operation perform through digital technology. IoT capabilities can help integrate a digital ecosystem of connected systems that provides users with relevant and updated data to make the most informed decision at all times.” Maplesden adds, “Set up real-time tracking to help identify delays. Receiving warning well ahead of time about potential issues can help supply chain managers act quickly and prevent or mitigate supply chain disruptions.”
• Evaluate and adjust procurement category strategic responsibilities. Another EY analyst suggestion involves procurement. “Transform procurement into a value generation function through timely reviews and adjust category strategic priorities to establish new business relationships with suppliers to align to a company’s overall supply chain objective. Organizations can introduce digital procurement technology to benefit from supplier social networks.”
• Invest in more collaborative and agile planning and fulfillment capabilities. According to EY analysts, “Today’s technology can provide more agility and collaboration within the enterprise. From IoT devices for demand sensing and goods movement tracking, there is a range of solutions that are fundamental. … It is time that companies quickly assess, recover and respond quickly to mitigate supply chain disruption as much as possible.”
Feather writes, “The late Charlie Munger once said, ‘I want to swim as well as I can against the tides. I’m not trying to predict the tides.’ Adopt that approach and mindset, and your future self, your company, and your company’s supply chain can all reap the benefits.” And, as Cecere insists, companies need to sense, respond, and adapt more capably than they do today. There are AI solutions that can help companies become more resilient.
Footnotes
[1] Joseph Shamir, “2020: Uncertainty calls out for resilience,” Supply Chain Digital, 30 November 2019.
[2] Matt Stekier and Aaron Ennest, “Supply Chain Resiliency and Strengthening Supply Chains,” Global Trade, 27 August 2024.
[3] Lora Cecere, “Supply Chain Resilience. Really?” Supply Chain Shaman, 7 December 2023.
[4] Nathan Feather, “Principles for supply chain resilience in 2024 and beyond,” Fast Company, 30 January 2024.
[5] Paul Maplesden, “7 techniques to build supply chain resilience,” TechTarget, 29 May 2020.
[6] Sean Galea-Pace, “EY: five ways to build a resilient supply chain,” Supply Chain Digital, 19 March 2020.